MATERFLOW @ FORMNEXT 2020
”Formnext is a leading global trade fair dedicated to additive manufacturing and industrial 3D printing.”
Under normal circumstances Frankfurt would have been the go-to place for additive manufacturing community in mid November but this year the stage was set, as expected, virtually. The trade fair casted foresights and innovations through screens around the world for three days offering opinions from leading AM companies and experts.
We were also digitally present. Here’s our take on the top topics from Formnext 2020 for the coming years of additive manufacturing and industrial 3D printing.
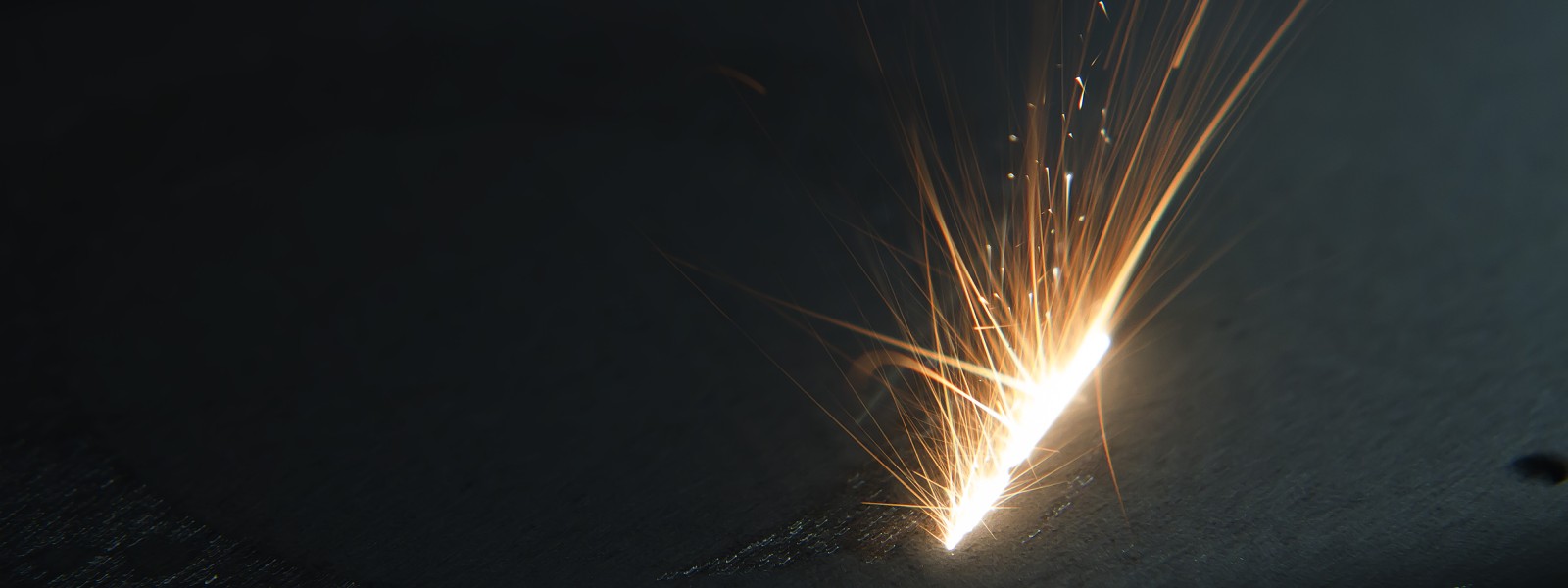
1. LOCALISED MANUFACTURING AND SUPPLY CHAINS
As Covid has so cruelly shown us, we cannot rely so heavily on the Chinese manufacturing industry or global supply chains in general. During the last some years the manufacturing of all sorts of components and industrial equipment has been taken over by China. Problems with product availability and shipping were felt around the world when Covid hit and supply chains broke down.
The concepts of localised manufacturing, smart factories and on-demand production kept popping up in panel discussions and expert opinions all through Formnext. These concepts have been industry favourites for a long time but are more relevant now than ever before. When key components, parts or products for business operations are manufactured or can be manufactured locally according to need i.e. on-demand, the need for complex supply chains and massive warehousing is reduced significantly. This also reduces the effects on climate as shipping stuff from one continent to another becomes more and more unnecessary.
Smart factories, or smart manufacturing, brings the production close to the end-user cutting out excessive logistics and lead times. This works particularly well with on-demand spare parts. An example setting adaptation of on-site production comes from AM forerunner Siemens Mobility Services. Siemens has extended their 3D printed spare parts program to railway industry including local manufacturing of maintenance parts for the German and UK rail industries. They are now expanding rail maintenance operations to Russia and will not only construct 13 new vehicles for RZD, a Russian train company, which already has a fleet of 16 trains in its high speed rail (HSR) line, but also maintain and service them over the next 30 years.
Some experts at Formnext painted a grand vision for localised manufacturing to include a chain of smart factories across continents to fulfil the needs that different industries have. Whether or not this factory chain concept is viable, doable or reasonable remains to be seen. What is certain though is the fact that industrial scale 3D printing is already a viable and cost-effective option to manufacture products in small series or even in mass. Instead of a chain of smart factories around the globe we might see the growth of a global networks of smaller local operators collaborating under unified platform, ones like these initiatives by Siemens and Xometry.
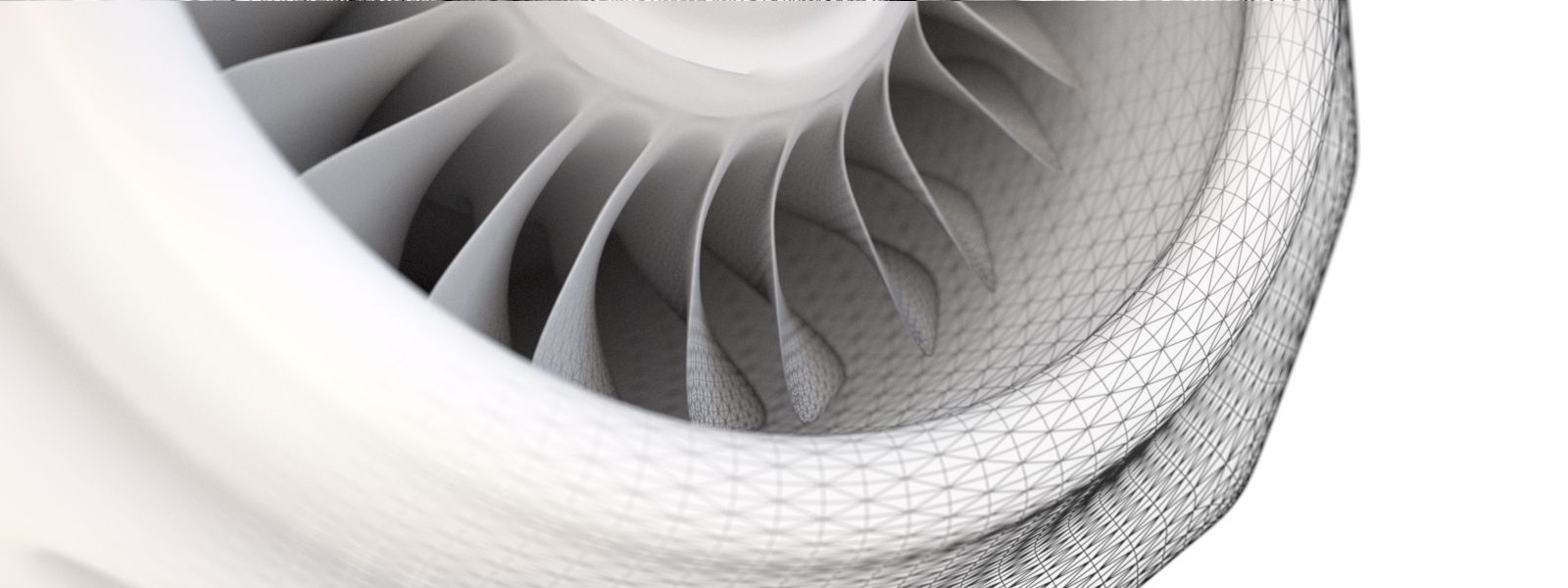
2. SUSTAINABILITY AND CIRCULAR ECONOMY
The megatrends stated above were front and center at Formnext. And no wonder. Additive manufacturing can and probably will be key in the circular economy age and riding the sustainability wave. Many panelists kept repeating the oldies but goldies “Compared to conventional manufacturing methods like milling 3D printing is a very sustainable method since you don’t waste any material when manufacturing products” or “Localised additive manufacturing is more ecological than shipping products around the world from China”.
Both goldies are true, but very little was said about the ecological downsides of 3D printing, the elephant in the room being how most of the plastic powders used in selective laser sintering technique go straight to trash after production without any chance to recycle. However, as we know it, some positive development is happening in this department. Also the use of biomass and bio print materials is gaining some ground. With metal powders and selective laser melting technique the powder reuse is much more efficient, and converting scrap metal into raw material for printing is already happening.
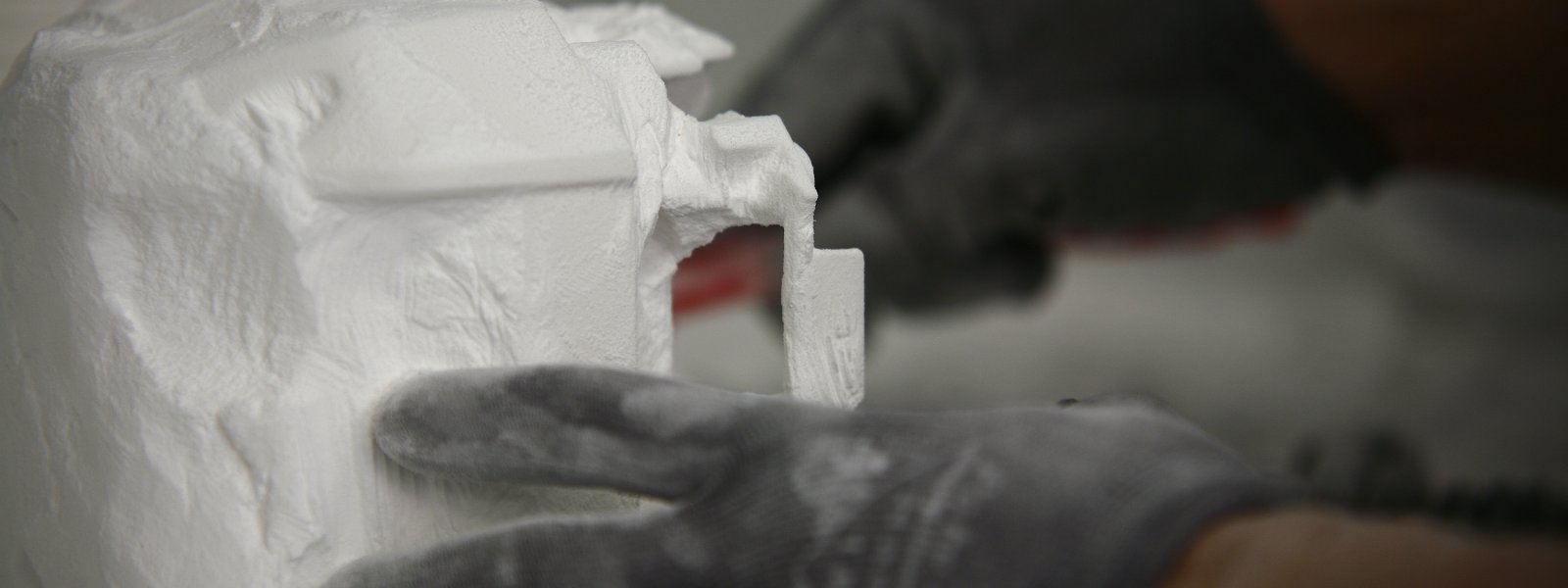
3. IMPROVING POST PROCESSING, ADDING AUTOMATION, COST-EFFICIENCY
Post printing processes still require hands-on craftsmanship. It takes time to clean the printed parts from excess material, and also, if necessary, surface treatments by polishing, dyeing, coating or painting require extra work. Based on many expert talks at Formnext the importance of post processing is well recognised in relation to the overall cost-effectiveness.
There’s already a lot of automation available that improves efficiency and speed, and it’s becoming easier to mechanically clean and surface-treat smaller parts, especially those that are manufactured in large quantities. The reduction in handicrafts in post processing has a direct effect on delivery times and the unit costs of parts. In our next newsletter, we’ll tell you more about the post processing services that we here at Materflow can offer.
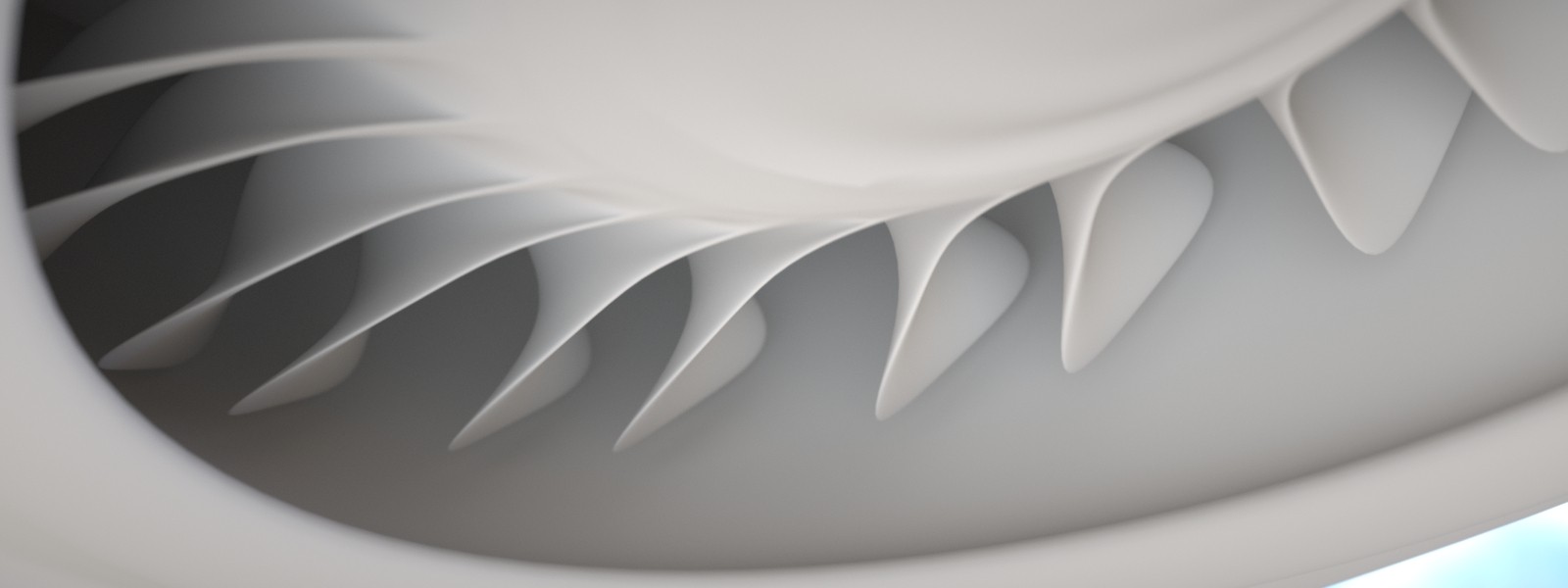
”DO WE NEED A CHANGE IN THE MINDSET OF THE USER INDUSTRIES?”
A good question from a main stage panel discussion during the opening day of Formnext. Industrial 3D printing is not a cure to every manufacturing ill, but you cannot deny its effects on supply chains or the way products are being designed and manufactured now and in the future. The AM industry is geared towards growth, innovation, and scalable as well as sustainable solutions. But the AM industry itself is not enough. To implement these possibilities we need forward looking minds that are willing to find competitive edge, try new things, and change some of the old ways of thinking and doing.
Some recommendations from Formnext 2020:
ADDITIVE MANUFACTURING AND ITS EFFECTS ON PRODUCT DESIGN AND PRODUCTION
HOW TO IDENTIFY SPARE PARTS FOR SERIAL 3D PRINTING?
Materflow designs and manufactures 3D printed metal and plastic parts for industrial use. Our customers operate in the industrial sector with ambitions in developing their products, supply chains, and processes towards more profitable and sustainable solutions. In addition to 3D printing services we help our customers develop and implement 3D printing into their design and engineering processes.