A New Era in 3D Printing Post-Processing: AMT PostPro SFX Vapor Smoothing Machine
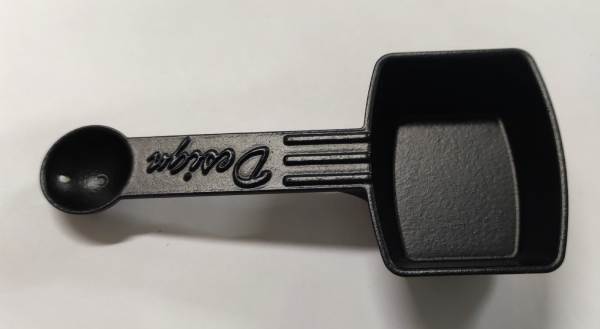
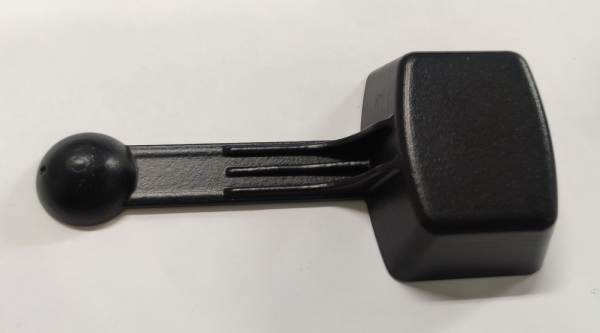
In July, Materflow received the much-anticipated AMT PostPro SFX vapor smoothing machine, a cutting-edge solution utilizing green chemistry technology.
“Finally, we have a chemical polishing machine that meets our safety standards and is environmentally friendly,” says Sami Mattila from Materflow.
“The reason we only acquired the machine now is that it incorporates ‘new green chemistry,’ significantly reducing its hazard level. Previously, chemical polishing systems used hexafluoroisopropanol (HFIP) as a solvent, which we did not want anywhere near our facilities due to its risks,” Mattila explains.
Specifications of the PostPro SFX Vapor Smoothing Machine:
- Process chamber dimensions: 190 x 320 x 190 mm
- Working solution: Biodegradable, environmentally friendly
- Certifications: FDA-approved, biocompatible, recyclable
The machine enhances surface quality, seals porosity, and improves durability and hygiene of parts. More details can be found on the manufacturer’s website.
Once the machine is unpacked and installed, Materflow plans to dedicate the first two weeks to testing it primarily with PA12 plastic. “Initially, we aim to use it for PA12 materials. Later, as we gain more experience, we may expand its use to other materials,” Mattila adds.
Vapor Smoothing, Also Known as Chemical Polishing
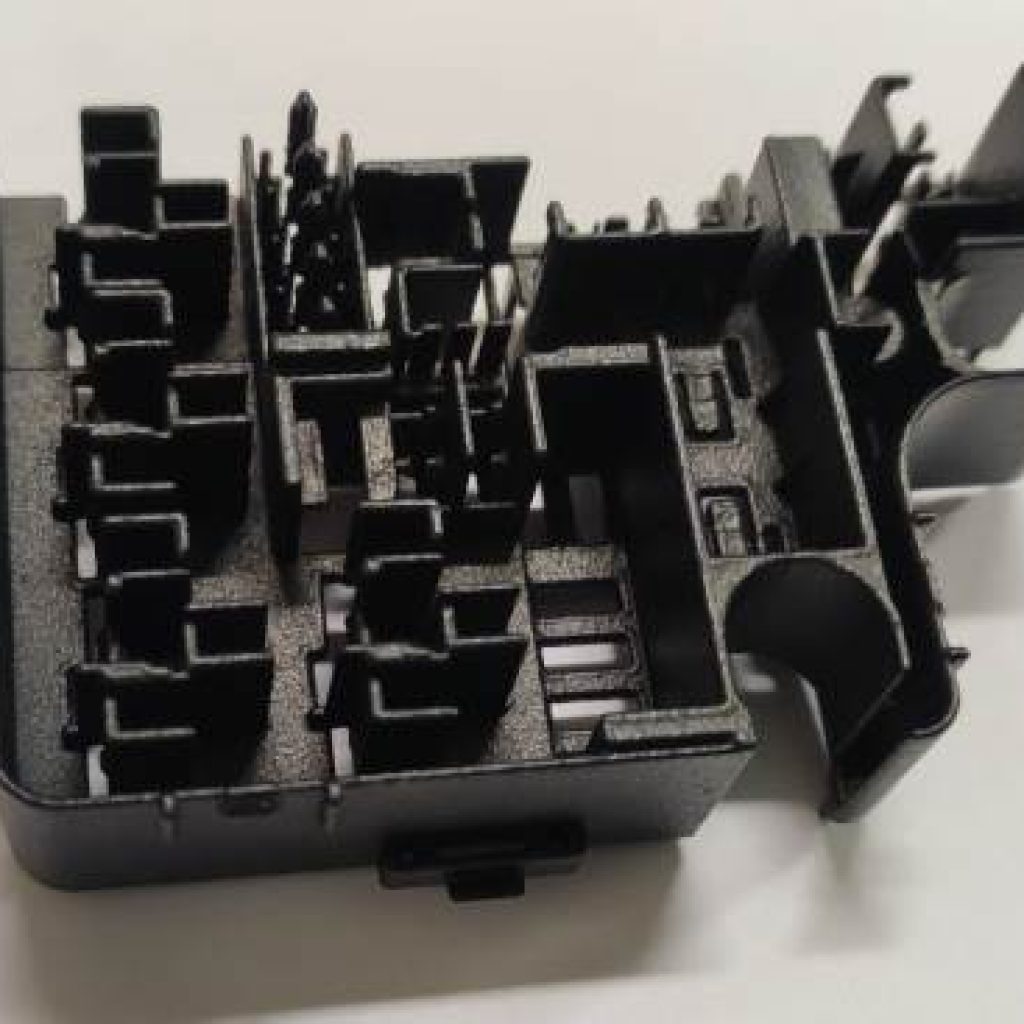
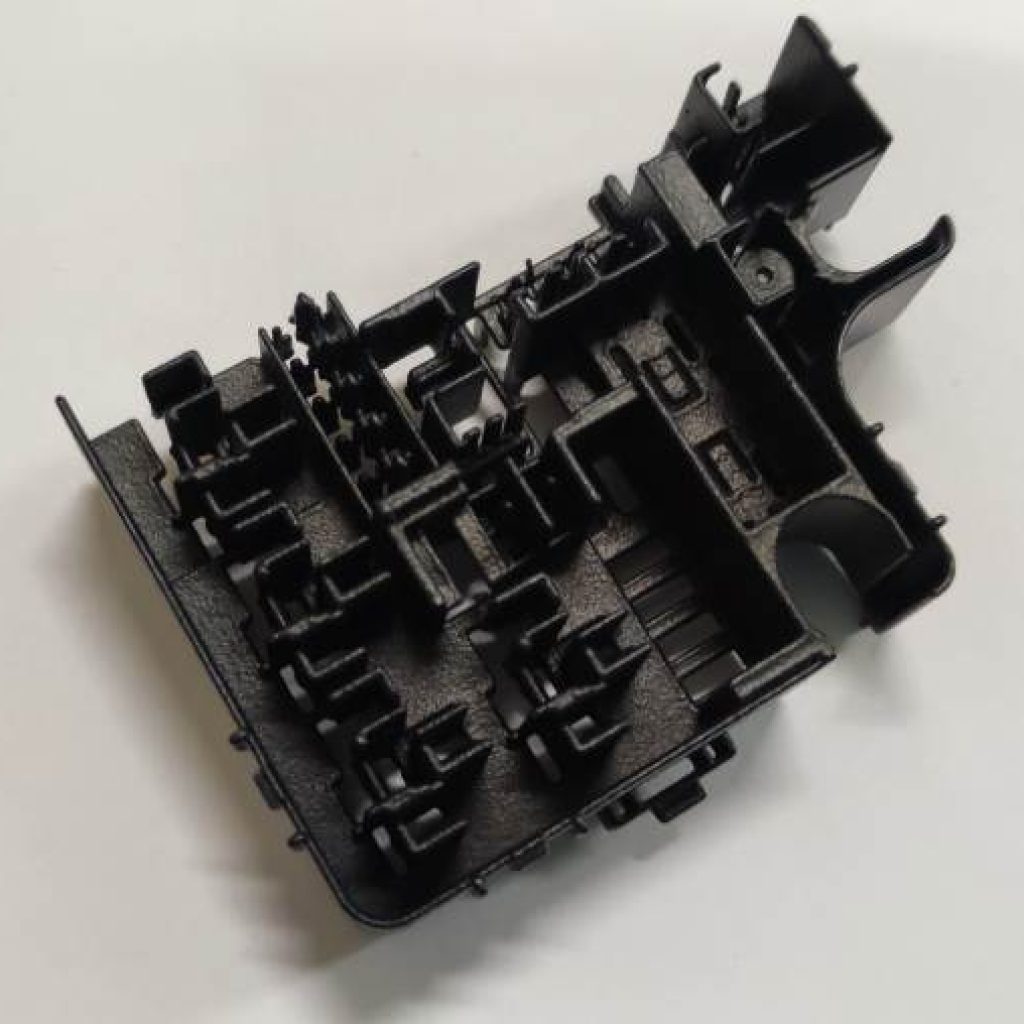
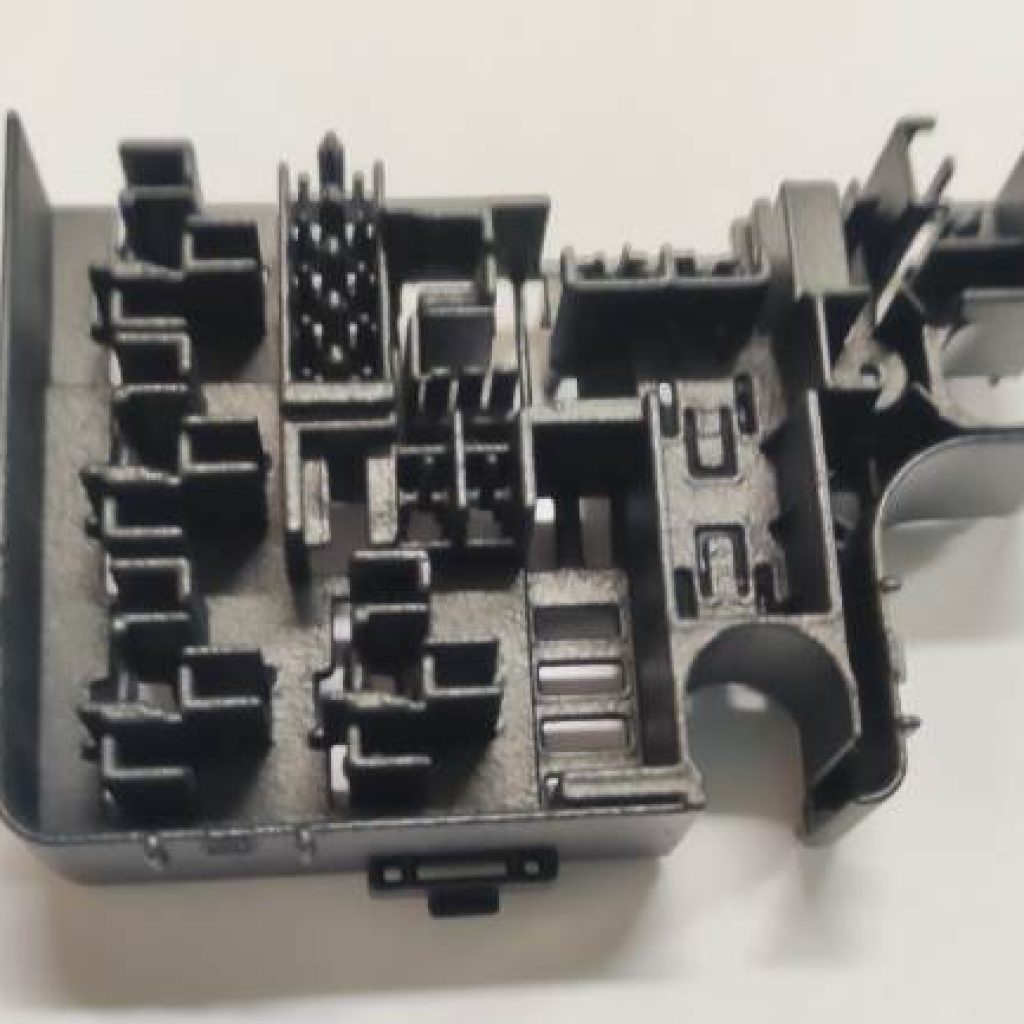
3D-printed parts are not immediately ready for all applications straight out of the printer. Their rough and porous surface limits functionality and usability, necessitating post-processing.
- Appearance and Functionality: After polishing, the surface becomes smoother and more visually appealing.
- Durability: The tensile strength and elongation at break of the parts improve, reducing the risk of damage even under heavy use.
- Hygiene: A smooth surface is easy to clean, and the closure of surface pores prevents bacterial growth.
“After chemical polishing, the tactile feel of the part is smooth and pleasant. We tested a chemically polished bus armrest with a modeled leather texture, and it felt almost like synthetic leather!”
– Sami Mattila
Applications
Chemical polishing is ideal for:
- Food industry parts
- Chemical industry (laboratory products)
- Parts in direct contact with people
- Components requiring cleanliness
- Visual elements
- Parts currently requiring painting
“After chemical polishing, the tactile feel of the part is smooth and pleasant. At a trade show, we had the chance to try a chemically polished plastic bus seat—it felt as good as faux leather,” Mattila recalls.
Chemical polishing is suitable for small parts in series and can also be applied to single, larger components.
Potential Challenges – Consider These in the Design Phase
Chemical polishing also has its limitations. During our testing phase, we have observed the following factors:
- Thin Walls May Warp
- The vaporized chemicals and the heat generated in the process can cause deformations in thin structures. This can be a significant challenge, especially in complex designs with very thin walls. The recommended wall thickness is 1 mm or more.
- Yellowing of White Parts
- If a part is printed in white, it may experience slight yellowing during the process. In design and material selection, it is important to consider that maintaining a 100% pure white appearance can be challenging.
- Dimensional Accuracy May Decrease
- Chemical polishing “melts” the surface at a microscopic level, smoothing and rounding it. While this effect is often desirable, parts with tight tolerance requirements may experience slight dimensional deviations. Maximum measured dimensional change: 0.4%.
- Sharp Edges Will Round Off
- As surfaces become smoother, the process also tends to round off edges and corners. If highly precise angles are required, this should be considered before polishing.
- Possible Surface Runs
- In complex geometries, vapor condensate may accumulate unevenly, leading to minor surface runs or irregularities. However, adjusting process settings and part orientation can help minimize these effects.
These factors do not typically prevent polishing but can affect the final product. That’s why test pieces are created for each project to optimize both the printing and polishing parameters.
At Materflow, we’re excited about this new investment, which introduces a more eco-friendly and efficient way to finish 3D-printed parts. Follow our blog for updates on test results and application examples!